What is Gypsum | How Gypsum is Processed
Definition of Gypsum
Gypsum ( CaSO4·2H2O) is a natural monoclinic minera, Its main chemical component is calcium sulfate hydrate, which is widely distributed in the salt lake sediments formed by evaporation and widely used as industrial materials and building materials.
History of Gypsum
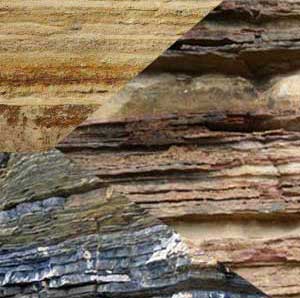
Gypsum is a kind of monocrystalline mineral, which often exists in the form of sedimentary rock
The English word for plaster is “Gypsum”, and German is “Gyps”. It all comes from the Greek γύψος (gypsos), and then the Latin word is “gypsus”. At that time, it didn’t mean gypsumin the modern sense, but meant something like moonstone.
Gypsum was used as a building material in the Neolithic Age and was used for interior decoration in Anatolia (now in Turkey) in 7000 BC. Evidence of the use of plaster was later found in Sumir and Babylon sites, such as Jericho in 6000 BC (now in Israel) and Uluk in 3000 BC (now in Iraq). The Pyramid of Khufu and the Sphinx, built in 2500 BC, used gypsum mortar as a cementitious material to bond and masonry stones.
Properties of Gypsum
Gypsum is a very common soft sulfate mineral, which can be easily identified by its hardness, cleavage and solubility in water:
Properties | Value | Properties | Value |
Name | Gypsum | Melting | 1350~1375℃ |
Formula | CaSO4·2H2O | Solubility | soluble in water |
Molecular | 172 | Cleavage | Perfect |
Colour | White, colorless, or yellow-red | Hardness | 2 mohs |
Lustre | Vitreous, Silky, Pearly | Tenacity | Flexible |
Transparency | Transparent, Translucent, Opaque | Density | 2.31~2.33 g/cm3 |
Streak | White | Crystal State | Plate, fibrous, bulk or fine grained |
Crystal | Monoclinic | Application | Architectural, Medical |
Classification of Gypsum
Gypsum usually refers to two kinds of minerals: raw gypsum and anhydrite.
Raw Gypsum is calcium sulfate dihydrate ((Ca (SO4) 2H2O), also known as gypsum dihydrate, gypsum or gypsum, composition CaO (32.6%), SO3 (46.5%), H2O+ (20.9%), monoclinic system, crystal is plate-like, usually dense block or fiber, white or gray, red, brown, vitreous or silky luster, Mohs hardness is 2, density 2.3g/cm3.
Anhydrite is anhydrous calcium sulfate (Ca (SO4)), theoretical component CaO (41.2%), SSO3 (58.8%), orthorhombic system, crystal is plate, usually dense block or granular, white, grayish white, vitreous luster, Morse hardness is 3 – 3.5, density 2.8~3.0g/cm3.
Raw gypsum and anhydrite are often produced together, and anhydrite can be formed by calcining gypsum at 400 – 500 °C.
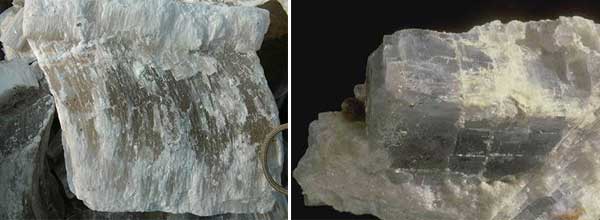
Gypsum vs Anhydrite
How is Gypsum Formed
Gypsum is a widely distributed mineral, which is mainly formed by sedimentation and weathering, and a few are found in hydrothermal sulphide deposits. Gypsum usually can be fond in the form of crystals or deposits beds.
Gypsum formed in sea basins and lake basins is formed by evaporation of brine or hydration of anhydrite; symbiosis with anhydrite, gypsum, etc. It is layered or lenticular in the interlayer of limestone, red shale, marl and sandy clay. The gypsum in the oxidation zone of sulphide deposits is mainly caused by sulfides.
Distribution of Gypsum
The world’s largest producer of gypsum is the United States. In the United States, gypsum deposits are distributed in 22 states with a total of 69 mines, with the largest producing area in Fort Dodge, Iowa, followed by Canada. France takes the lead in European gypsum production, followed by Germany, the United Kingdom and Spain.
Use of Gypsum
Gypsum is a widely used industrial material and building material. Gypsum (CaSO4 ·2H2O) can be calcined and grinded to obtain β-type hemihydrate gypsum (2CaSO4 ·H2O), that is, building gypsum, also known as cooked gypsum or plaster. The model gypsum can be obtained when the calcination temperature is 190 °C, and its fineness and whiteness are higher than that of building gypsum. If raw gypsum is calcined at 400 °C or above 800 °C, floor gypsum can be obtained, its setting and hardening are slow, but the strength, wear resistance and water resistance of hardened gypsum are better than that of ordinary building gypsum.
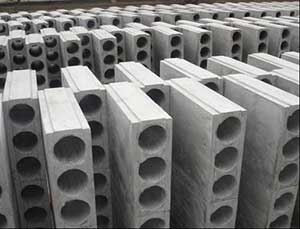
Construction Gypsum
- Building Gypsum: Mostly used in building mold ash, painting, masonry mortar and all kinds of gypsum products.
- Model Gypsum: less impurities, white color, mainly used for ceramic culture process, a small amount for decorative relief.
- Floor Gypsum: Mainly used for demanding mold ash engineering, decorative products and plasterboard.
- Whitewash Gypsum: Made of cementing material with appropriate amount of retarder, water-retaining agent and other chemical admixtures.
In addition, gypsum can also be used in the manufacture of cement, sulfuric acid, soil improvers, food coagulants, pesticide diluents as well as medical and cosmetology.
How is Gypsum Processed
The raw material of gypsum powder is natural gypsum ore, and the production process of gypsum powder is mainly divided into 5 stages: crushing, screening, grinding, calcination, storage and transportation.
- Crushing: The mined gypsum ore raw material enters the crusher through vibrating feeder, and the crusher break the large-size gypsum ore into small particles smaller than 30mm, and then waits for further screening treatment.
- Screening: Use a vibrating screen to separate incomplete large particles and impurities that mixed in crushed gypsum. Gypsum with suitable available size can be separated by controlling the diameter of sieve hole, which can be used as cement additive for sale. Or go straight to the next stage.
- Grinding: The screened gypsums are fed into the grinding mill uniformly and continuously by vibratory feeders for grinding. The ground gypsum powder is blown out by the air flow bulged by the mill blower and graded by the separator machine on the mill. The fineness qualified powder is collected by hydrocyclone and discharged through the powder outlet tube, is know as land plaster. Land plaster is sent by screw conveyor. As a soil conditioner, or transported to calcination.
- Calcination: Calcination mainly uses the direct contact between high-temperature hot flue gas of boiling furnace and gypsum raw materials to complete the calcination and dehydration of gypsum powder. The structure and characteristics of dehydrated gypsum are also different under different heating conditions.
- Storage Transportation: The calcined qualified gypsum powder is sent to the clinker warehouse for storage or into the workshop to produce gypsum board, cement and other gypsum products.
Subject: Inquiry for Gypsum Powder Plaster Manufacturing Plant with 1000 Tons Daily Production Capacity
Dear Sir / Madam,
I hope this message finds you well. I am writing to express my interest in getting detailed information and a quote with detailed proposal for a gypsum powder plaster manufacturing plant with a daily production capacity of 1,000 tons.
Key Requirements:
1. Production Capacity:
• The plant should be capable of producing 1,000 tons of gypsum powder plaster per day.
2. Technology and Equipment:
• Please provide detailed specifications of the machinery and technology used in the production process.
• Information on automation levels, energy consumption, and efficiency metrics.
• Details on the quality control systems in place to ensure consistent product quality.
3. Raw Material Requirements:
• What are the raw material specifications and quantities required to achieve the mentioned production capacity?
• Details on any specific raw material suppliers or grades preferred.
4. Plant Layout and Design:
• Suggested layout for optimal operation and space utilization.
• Any specific environmental considerations or certifications that the plant design adheres to.
5. Utilities and Infrastructure:
• Requirements for power, water, and other utilities.
• Any other infrastructure needs, such as storage facilities, transportation logistics, etc.
6. Labor and Operational Needs:
• Recommended workforce for efficient operation of the plant.
• Training and technical support provided for plant operations and maintenance.
7. Installation and Commissioning:
• Detailed timeline for installation and commissioning of the plant.
• Scope of services provided during the installation phase, including site preparation, equipment setup, and testing.
8. Maintenance and After-Sales Support:
• Information on warranty, regular maintenance schedules, and availability of spare parts.
• Details on after-sales support and customer service.
9. Cost and Payment Terms:
• Detailed breakdown of the costs involved in setting up the plant.
• Payment terms and any financing options available.
10. Compliance and Certification:
• Compliance with local and international standards for manufacturing gypsum powder plaster.
• Information on any certifications that the plant equipment or process holds.
11. Project References:
• Case studies or references from similar projects undertaken, especially those with similar production abilities.
12. Additional Information:
• Any recommendations or other options that could enhance the operation or efficiency of the plant.
I would appreciate it if you could provide this information at your earliest convenience, along with any brochures, catalogs, or technical documents that could help in understanding the plant’s capabilities.
Please feel free to contact me directly at +228 9008 9966 or via email at rohit.motaparti@diamondcement.com if you need any other details or clarification.
Thank you for your attention to this inquiry. I look forward to your prompt response.
Best regards,
Rohit Motaparti
Director
Diamond Cement GhanaLimited
Aflao, Ghana
I would like to know the way to processing the Gypsum Powder
Ok, Mr Tahliil, the grinding mill manufacturer will contact you very soon!
Grinding, processing equipments
Thanks for the effort and all the info
But is there a difference between plaster and gypsum, I hope to find an answer for you
Thank you very much, glad to hear from you, more information send to beidoou2020@outlook.com please.