5 Tips of Vibrating Screen Problems & Solutions
There are many kinds of vibration screens, such as electromagnetic vibration screens, circular vibration screens, linear vibration screens, etc. The latter two belong to inertial vibration screens, which are commonly referred to as vibration screens. In daily production, vibration screen will encounter a variety of problems, such as poor screening quality, bearing overheating, abnormal sound, wrong technical indicators and so on.
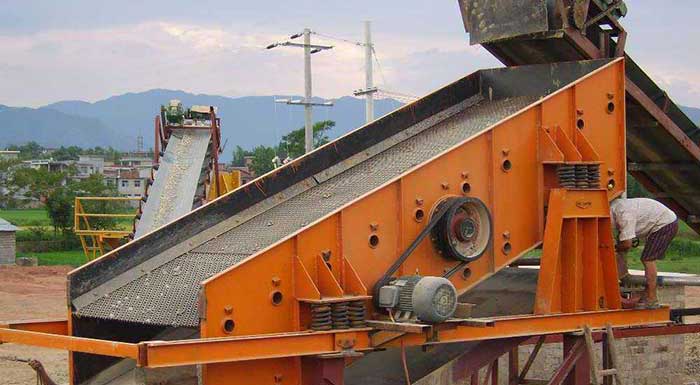
1. Poor screening quality
There are many factors affecting the screening effect, including the nature of feeding, equipment factors, operation factors and so on. The reasons for poor screening quality include blocking of sieve hole, serious wear of sieve hole, uneven feeding of sieve, too thick material on sieve and insufficient inclination of sieve surface.
1) Screen hole blockage
When the mud content and water content in the feed are high, the material will stick to the sieve hole and block the sieve hole. At this time, the sieve hole should be cleaned first, and then the spray amount and the inclination angle of the sieve surface should be adjusted appropriately.
2) serious wear of screen hole
When the screen is used for a long time, the wear of the screen hole will be serious and the screening effect will be seriously affected. At this time, the wear screen hole should be repaired. When the wear situation is very serious, the replacement of screen mesh should be considered.
3) Non-uniform feeding of sieve
When the feeding trough of the sieve is too narrow, the material can not be uniformly distributed along the whole sieve surface, which makes the sieve surface inefficient to use, and will affect the screening effect. At this time, the width of feeding trough should be adjusted to make the feeding of sieve uniform.
4) too thick material on screen
The excessive thickness of material on screen may be caused by the increase of feeding quantity, blocking of screen hole and small inclination angle of screen surface. At this time, it should be adjusted according to the specific situation.
5) insufficient inclination of screen surface
For the circular vibrating screen, the most common reason for the poor screening effect is the inadequate inclination of the screen surface, so it is necessary to pad the back support. In practical application, the inclination angle of screen surface is more suitable when it is 20 degrees. The inclination angle of circular vibrating screen is generally 16-20 degrees. If the inclination angle is lower than 16 degrees, the phenomenon that the material on the screen is not moving smoothly or rolling upward will occur.
6) The motion direction of eccentric block is not in the same phase
For linear vibrating screen and high frequency vibrating screen, the poor screening quality may be related to the movement direction of eccentric block, because two groups of eccentric blocks with the same mass need to rotate in self-synchronization and reverse direction to produce a single exciting force along the vibration direction at each instant, which has a fixed angle with the horizontal direction, so that the screen box can move in a reciprocating straight line. If not in the same phase, the direction of excitation force and direction of vibration will not overlap, and the effect of efficient screening will not be achieved.
2. Bearing overheating
Generally speaking, the bearing temperature should be kept between 35 and 60. If the bearing temperature is too high during the test run, there may be the following reasons:
1) too small radial clearance of bearing
Because the bearing on the vibrating screen bears a large load, a high frequency, and the load is always changing, the bearing must adopt a large clearance. If the bearing with ordinary clearance is used, the outer ring of the bearing must be grinded again to make it a large clearance.
2) too tight top of bearing cover
There must be a clearance between the cover and the outer ring of the bearing to ensure the normal heat dissipation and certain axial movement of the bearing. The clearance can be adjusted by a gasket between the end cap and the bearing seat.
3) Bearing oil shortage or excessive, oil pollution or inconsistency
At this time, the bearings need to be oiled, cleaned, replaced and sealed to check the quality of oil and oil injection. In addition, there may be bearing wear or bearing quality problems.
3. Abnormal sound when the sieve is running
The possible causes of abnormal sound during the operation of sieve are spring damage, bearing wear, bolt loosening of fixed bearing, unstretched screen, etc.
1) Spring damage
When the spring is damaged, there will be greater noise. At this time, the spring should be replaced in time to prevent production accidents.
2) Bearing wear
When bearing wear is serious, it will produce great noise. At this time, the machine should be stopped and the bearing should be replaced in time.
3) Bolt loosening of fixed bearings
The loosening of the bolt of the fixed bearing will cause abnormal sound when the sieve is running. The bolt should be tightened in time at this time.
4) Untightened screen
When the screen is not tightened, it will make the sound abnormal when the screen is running, and affect the screening effect of the screen. At this time, the screen should be tightened in time.
4. Technical indicators do not meet the requirements
The technical indicators of the operation of the sieve include the rotational speed, vibration force, amplitude and frequency of the sieve, etc. Common fault types are: the screen can not start or the amplitude is too small, the speed is not enough, the vibration force is weak, the four-point amplitude is inconsistent, and so on.
1) The sieve cannot start or its amplitude is too small.
When the vibration screen can not start or the amplitude is too small, the first consideration should be whether there is an electrical fault. Damage of motor and insufficient voltage can lead to faults. When there are no problems in the above aspects, we should start with the mechanical aspects. Whether the material on the screen surface is heavily accumulated or not, if so, it should be removed in time; whether the bolts on the coupling of the exciter fall off or not, whether the grease is caked; if so, the bolts should be tightened in time and the grease should be replaced.
2) Insufficient rotational speed of sieve
Insufficient rotational speed may be the electrical reason. At this time, we should find out the reason and deal with it in time. It may also be that the transmission tape is too loose. At this time, we should tighten the transmission tape.
3) The Vibration Force of the Screen is Weak
Weak vibration may be due to incorrect or too light weight on the flywheel, so the weight on the flywheel should be adjusted at this time.
4) The amplitude of four points of the sieve is inconsistent
The inconsistency of four-point amplitude of sieve may be caused by the asynchronism of two exciters on the same axis or material segregation. At this time, adjustments should be made to make the two exciters work synchronously and eliminate material segregation in time.
5. Severe or damaged parts of sieve
Some parts of the sieve will be worn seriously or even broken after being used for a long time. Common faults are pipe beam fracture, cross beam fracture, screen frame fracture and so on.
1) Pipe Beam Fracture
(a) The thin wall of pipe girder may lead to fracture. At this time, the same type of thick wall pipe or the first type of pipe girder should be selected, but it should not be too large or too thick, because this will increase the vibration quality of the sieve and bring many problems;
B) There must be horizontal and vertical pressure strips at the joints of the sieve plates of dehydration and de-mediation screens. If there is no longitudinal pressure strip, water will leak from the gap between the sieve screens and wash down the pipe girders, which are easy to break at the scouring point.
C) The wider the sieve is, the easier the pipe beam will break. According to experience, when the sieve width exceeds 3 m, it is better to use double channels.
D) If the fracture of the pipe beam is not serious, in order not to affect production, the pipe beam can be repaired to continue to use. When repairing, the weld should be along the longitudinal direction of the pipe beam, and no transverse weld must be allowed, otherwise the pipe beam is more likely to fracture from the transverse weld.
2) Beam fracture
Cross beam fracture is mostly due to the long working time at critical frequency, a large number of high-strength bolts to tighten the side plate are relaxed, serious deformation of the spring makes a great difference between left and right, or it may be that the weight error of eccentric block is too large, causing structural damage and cross beam fracture. At this time, the damaged structural parts and beams should be replaced, bolts should be tightened, and the quality of eccentric blocks should be adjusted.
3) Fracture of screen frame
The sieve frame is liable to break because of tremor. The best way to solve this problem is to thicken the side plate or add additional plate to the local area of the side plate near the exciter to enhance the rigidity of the whole sieve frame.
Hi
I am just completed the design of a maize cobs briquettes production plant. In the plant I have included a vibrating screen. The purpose of the vibrating screen is to clean unprocessed maize cobs before it goes into the grinder for size reduction.
It is planned that the vibrating screen shall be of an enclosed type to eliminate dust problems and have a self-cleaning mechanism with suitable waste collection and disposal facility. Suitable screen type and size shall be used to eliminate extraneous materials like sand/soil and stones from fields where maize cobs will be sourced and picked.
The vibrating screen shall also be able to remove stones larger than the openings on the screen mesh that may be picked along with maize cobs from fields.
The vibrating screen shall have a capacity of 2.5 T/hr., be suitable for a 400 V, AC, 50 Hz power system and be complete with necessary monitoring, control and protection devices and necessary attachments.
Could you, if you can, please send me a quotation for a vibrating screen that meet the above specification. The quotation shall indicate the following:
i) Type of unit
ii) Type of material used
iii) Screen mesh size
iv) No. of screens
v) Dimensions of the unit
vi) Total power requirements for the unit (kW)
vii) Total cost of unit (US$)
viii) Any other special requirements/specifications
Rgds
Mwenda C
Thanks for explaining that you should replace screen mesh if it has been used for a long time. This makes sense, because that way you can save money by getting more efficient results. I’ll have to look for a wire mesh screen.